Spray Foam Insulation
Advantages:
Foam expands, so it seals up leaks and gaps better than either cellulose or batts. It’s easy to install in tight spaces, and can be installed in wall cavities without removing the drywall. Los Angeles Insulated Spray-foam comes in all shapes, sizes, prices, and R-values. The two general categories are closed-cell and open-cell. Closed-cell foam has a higher R-value (about 6R per inch), but is more expensive than open-cell (which is about 3.5R per inch). For an equivalent R-value, open-cell will generally be less expensive. The high R-value-per-inch of closed-cell foam makes it a good choice if you have limited space; it also prevents moisture transmission better than just about any other insulating material.
Disadvantages:
Foam is pricier than most other insulating materials to begin with, and it will need to be installed by a spray-foam contractor (no do-it-yourself option), raising the price even more. It also releases greenhouse gases during application (HCFC’s or HFC’s), so it’s not the greenest option. Some people have a chemical sensitivity to the spray foam after it has been installed.
Rigid Panel Insulation
Building Doctors offers rigid foam panel insulation for a variety of applications. Whether you're involved in a deep energy retrofit, a simple energy upgrade, or need rigid foam insulation for a new construction project, Building Doctors has you covered.
Rigid foam insulation has a number of advantages; while it's not a perfect insulation material for all jobs, there are a many situations in which it's the ideal insulation.
Types of Rigid Foam Insulation:
There are three basic foam insulation board products on the market produced under several different manufacturer names. The basic types of foam board insulation are expanded polystyrene, extruded polystyrene, and polyisocyanurate unfaced or foil faced.
Expanded Polystyrene Foam
Expanded polystyrene foam (EPS) is the least expensive and least used foam board product on the market. This product typically has an R value of 3.6 to 4.0 per inch of thickness. Expanded polystyrene insulation is similar to the foam used for packing “peanuts” and it’s typically used for insulated concrete forms also known as ICF’s. It is used sometimes on commercial buildings for roof and wall panel insulation, where it is typically sandwiched between light gauge metal.
Cost = Cheapest of the foam insulation boards.
Extruded Polystyrene Foam
Extruded polystyrene foam (XPS) also known as blue board or pink board comes in many different thicknesses and edge profiles. This insulation board is probably one of the most widely used foam board insulation products in the residential construction industry. XPS has an R value of 4.5 to 5.0 per inch of thickness.
This is the product that I typically use to insulate basement walls. It’s reasonably priced, light weight and easy to use. This product is also used to insulate the outside of foundation walls and even under slabs.
Cost = This product is the middle of the road for these types of foam board insulation products.
Polyisocyanurate and Polyurethane
Polyisocyanurate also known as polyiso is seen in all kinds of commercial building applications and more recently with residential building projects. Polyiso is typically used with a foil facing and it has an R value of 7.0 to 8.0 per inch of thickness. The reflective foil facing makes it an excellent insulation board when radiant heat is involved. The foil facing also makes it very easy to seal with good quality foil faced tapes.
Cost = Polyiso is the most expensive of the foam board insulation products however it’s the highest R value.
Polyurethane and polyisocyanurate are both closed-cell foams. They contain low-conductivity gases in the cells (usually one of the HCFC or CFC gases.) The higher R-Values (R 7.0 to 8.0) are the result of thermal resistance of the gases in the cells. This can lead to a couple of disadvantages including: off gassing of HCFC or CFC gases, and reduced R Value over time as the gas escapes.
Advantages of Rigid Foam Insulation:
Rigid insulation has a high R-value per inch, so it’s a practical solution for a high R-value where space is limited.
Disadvantages of Rigid Foam Insulation:
They can’t be retrofitted into existing walls without removing the drywall, and are susceptible to the same air-leakage problems as fiberglass batts and blankets. They need to be meticulously installed to limit gaps and air leaks, and they’re slightly more expensive than alternatives.
They can’t be retrofitted into existing walls without removing the drywall, and are susceptible to the same air-leakage problems as fiberglass batts.
We'd be happy to talk with you about which insulation product would be the best fit for your home.
Reflective Insulation & Radiant Barriers
Advantages:
Reflective insulation and radiant barriers serve primarily to reflect radiant heat, but do little to prevent heat transfer through convection. They’re highly useful in southern or warm climates where the main objective is to keep solar heat out of the building. They look like a big sheet of foil, and serve primarily to block solar heat, even though they’re applied internally. Here’s how: the sun heats the materials on a roof, for example. These materials, now hot, transfer heat through convection (heat moving through the material) and through radiation (heat emitted directly from material). The radiant barrier, which you could install by laying it on top of existing attic insulation, or by attaching it to the underside of the rafters, blocks the radiant heat, reflects it back into roofing material and keeps it out of your living space.
Disadvantages:
Doesn’t prevent convective heat transfer – so it won’t keep the heat inside in the winter. Reflective insulation does include a thin layer of material to prevent heat transfer through convection, and so has a small R-value (a radiant barrier has no R-value). Reflective insulation and radiant barriers thus serve as a supplement to bulk insulation (i.e. cellulose, spray-foam or fiberglass batts), but will not suffice on their own, particularly in cool climates.
Blown Insulation
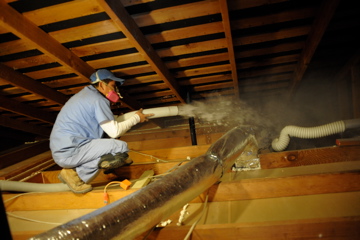
Can also be wet-sprayed (applied with a water-based adhesive).
Advantages:
Cellulose is made with up to 80% recycled material (shredded newspaper, mostly), it uses less energy than fiberglass to manufacture, it’s non-toxic, inexpensive, more effective than batts at sealing air leaks as well as nooks and crannies, flows around wall studs to increase the R-value of the entire wall, and it’s highly flame-retardant. It’s also easy to retrofit walls with dry-fill cellulose by cutting a small hole (which is later patched) in between each stud at the top of the wall and blowing in the insulation. You’ll also want to remove a piece of drywall at the bottom of the wall to make sure the cellulose has made its way all the way down. Cellulose is also good for retrofitting attics; if it’s distributed evenly you can be sure there are no gaps in the thermal barrier.
Disadvantages:
May absorb moisture, and can settle over time if not installed properly, both of which reduce its R-value. It’s heavier than fiberglass, so it may cause some ceilings to sag.
Batt & Blanket Fiberglass Insulation
Fiberglass batts and blankets are the most common type of insulation in U.S. homes, but not necessarily the best. Batts are pre-cut, whereas blankets come in a big roll. Cotton batts or “denim insulation” – non-toxic alternatives to fiberglass – are also available. The advantages and disadvantages below refer specifically to fiberglass batts and blankets.
Advantages:
Fire resistant, and won’t settle over time. Good for retrofitting an attic if there isn’t a lot of obstructions; just lay it on top of the existing insulation, and take care not to leave gaps or skimp out around the eaves. Fiberglass is inexpensive (compared to cotton batts, spray-foam or rigid insulation), and is comparable to cellulose in terms of R-value.
Disadvantages:
Can leave holes and gaps where air can circulate or condensation can occur, reducing R-value. A 3/4 air gap in batt insulation will result in a 80% reduction in the R-value of the insulation. Fiberglass particles pose a health threat during installation. It takes nearly 10 times as much energy to produce fiberglass insulation as it does to produce cellulose. You wouldn’t be able to retrofit existing walls by installing batts without first removing the drywall.